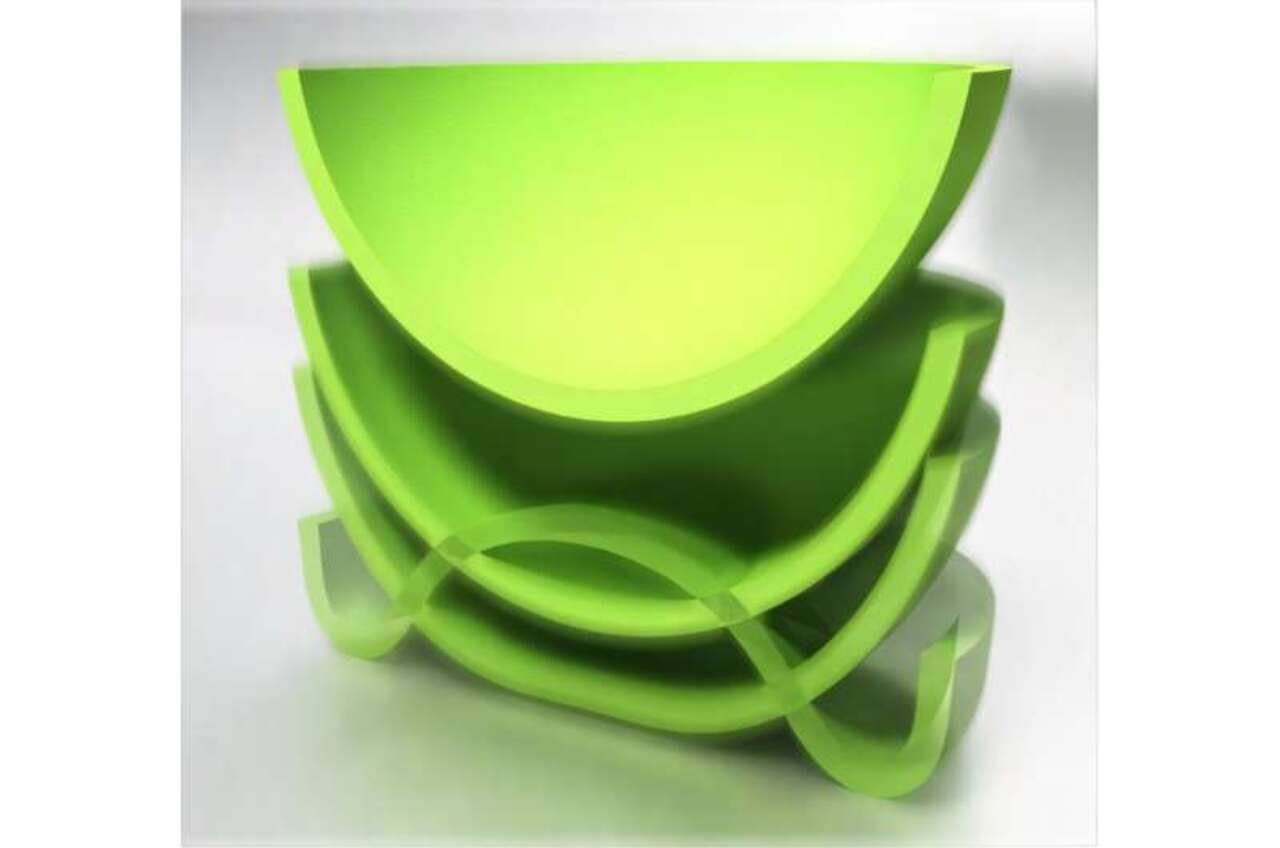
Inspired by a children’s toy, Japanese study creates formula that allows to accurately predict the jumps of soft and flexible robots
A simple toy has provided the foundation for a breakthrough in soft robotics. Inspired by a bouncy popper, researchers in Japan have found a way to make soft robots more agile and predictable.
The study was led by scientists from Keio University and Osaka University. They published the results in the journal Advanced Robotics Research .
The focus was to understand the physics behind the bouncing of thin hemispherical shells, a common structure used in soft robots.
Detailed study of jumping shells
The researchers fabricated several half-sphere-shaped shells made of silicone rubber. Using an experimental table with air pressure control, they observed how these structures deformed when bouncing.
To record everything, sensors tracked the rapid changes in the shape of the shells in real time. The team also used a technique called the Material Point Method (MPM) to accurately simulate this behavior.
These data revealed a crucial detail: the change in the shape of the contact area between the shell and the ground during the jump. This transition goes from a ring to a complete disk. This change, according to the scientists, is the key to understanding how energy is transferred to launch the shell upward.
Predictive formula for jump height
Based on this discovery, the researchers created a formula to predict jump height. The equation divides the movement into two parts: the initial lift and the final pop.
In tests, the formula produced results consistent with real measurements and simulations. This eliminates the need for old trial-and-error methods.
The main advance is in predictability. It is now possible to design jumping robots with greater precision, adapting each machine to its purpose.
This brings great benefits to robots used in search and rescue or environmental exploration missions, where terrain is challenging.
Applications beyond robotics
Researcher Tomohiko Sano noted that detailed analysis of individual elements, such as the jumping shell, could improve the entire robot system. He said the study marks a new phase in the development of theory-based designs.
Professor Ryuichi Tarumi, co-author of the study, said that understanding this type of structure helps to build more efficient robots, without having to test several parameters manually.
In addition to robotics, the data can also contribute to other areas. The team points to positive impacts in biomechanics, materials science and aerospace engineering.
This discovery represents an important advance for the future of lightweight and flexible machines.